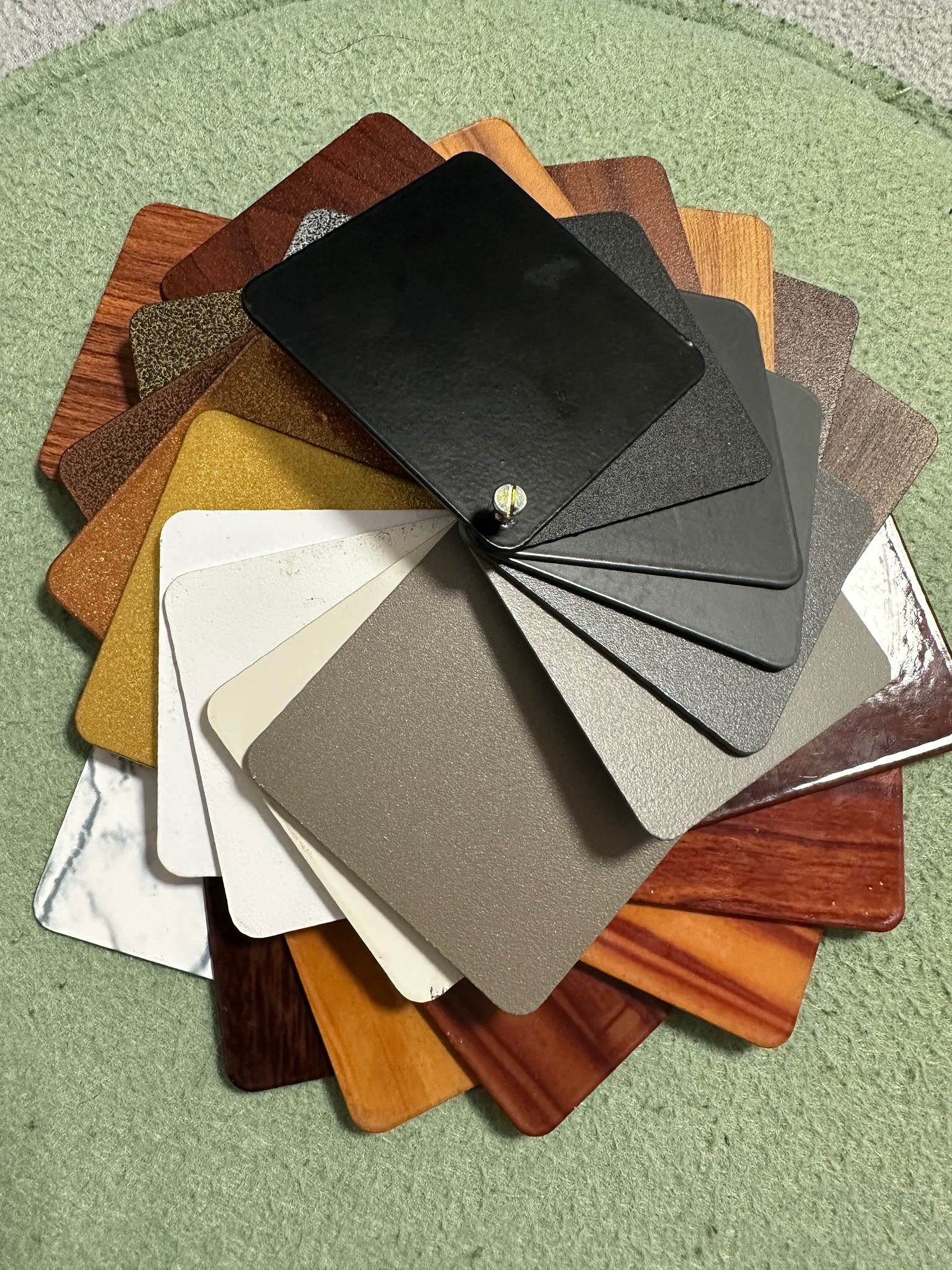
Understanding Powder Coating: A Revolutionary Surface Finishing Technique
In today’s industrial and manufacturing sectors, powder coating stands out as a premier surface finishing method. From automotive parts to household appliances, this advanced technology ensures products are not only visually appealing but also durable. Let’s dive into the essentials of powder coating and what makes it a preferred choice.
What is Powder Coating?
Powder coating is a dry finishing process that involves applying a powdered pigment to a surface and curing it under heat. Unlike traditional liquid paints, powder coating is solvent-free, making it an eco-friendly alternative. The powder is typically a mixture of finely ground particles of pigment and resin, electrostatically charged and sprayed onto a substrate.
Benefits of Powder Coating:
- Durability: Powder-coated surfaces are resistant to chipping, scratching, and fading, ensuring long-lasting protection.
- Eco-Friendly: It emits virtually no volatile organic compounds (VOCs), making it safer for the environment.
- Cost-Effective: Minimal waste, as overspray can often be recycled.
- Aesthetic Versatility: Available in a wide range of colors and finishes, including matte, glossy, textured, and metallic.
Applications of Powder Coating:
- Automotive: Wheels, bumpers, and other components.
- Construction: Window frames, railings, and structural elements.
- Appliances: Refrigerators, washers, and dryers.
- Furniture: Outdoor furniture, shelves, and lighting fixtures.
In conclusion, powder coating combines functionality and aesthetics, making it a go-to solution for industries seeking sustainable and high-quality finishes. Whether you’re a manufacturer or a consumer, understanding this innovative process can help you appreciate the value it brings to everyday products.
Powder Coating vs. Liquid Paint: Why Powder Coating Wins
When it comes to surface finishing, businesses and individuals often face the dilemma of choosing between powder coating and traditional liquid paint. While both have their merits, powder coating has steadily gained the upper hand in modern manufacturing. Let’s explore why.
Key Differences:
- Application Process:
- Powder Coating: Applied using an electrostatic spray gun, followed by curing under heat to create a smooth, even finish.
- Liquid Paint: Applied with brushes or sprayers and air-dried, often requiring multiple coats for uniformity.
- Durability: Powder coating forms a tough, durable layer that withstands harsh weather, chemicals, and abrasions. Liquid paint, on the other hand, is prone to chipping and peeling over time.
- Environmental Impact: Powder coating is VOC-free and generates minimal waste. Liquid paint contains solvents that release VOCs, contributing to air pollution.
Cost Analysis:
While the initial investment in powder coating equipment is higher, the long-term benefits, including reduced maintenance and waste, make it more cost-effective than liquid paint.
Aesthetic Appeal:
Powder coating offers superior finish consistency with a range of textures and colors that liquid paint struggles to achieve.
In summary, powder coating emerges as the winner in terms of durability, environmental safety, and aesthetic options. If you’re looking for a finishing process that balances quality and sustainability, powder coating is the clear choice.
The Powder Coating Process: Step-by-Step Guide
Powder coating is a meticulous process that transforms raw materials into visually stunning and durable products. Curious about how it works? Here’s a step-by-step guide to the powder coating process.
Step 1: Surface Preparation
The surface to be coated is thoroughly cleaned to remove any dirt, grease, or rust. This ensures that the powder coating adheres properly.
Step 2: Application
Electrostatic spray guns are used to apply the powder coating to the object. The powder particles are charged, causing them to stick to the surface of the object.
Step 3: Curing
Once the powder is applied, the object is heated in a curing oven. The heat melts the powder, which then forms a smooth and durable finish.
Step 4: Cooling and Inspection
The coated object is allowed to cool, and a thorough inspection is conducted to ensure the coating is even and free of defects.
- Adhesion testing
- Impact resistance
- Color and gloss checks
Benefits of a Well-Executed Process
- Enhanced durability
- Uniform and consistent finishes
- Reduced material waste
Powder coating is a blend of art and science, requiring precision at every stage. By following these steps, manufacturers can deliver products that are not only aesthetically pleasing but also built to last.